Конверсия углеводородов для утилизации попутных газов на
удалённых нефтяных промыслах в экологически чистые дизельное топливо и бензин.
В.С. Игумнов, И.О.
Тепляков, Вавилов С.Н., Разуванов, Гусева А.,
Кубриков К.Г., Мамайкин Д.С., Виноградов Д.А.
ОИВТАН, 125412, Москва, ул. Ижорская, 13, стр.2
Объединённый институт высоких температур РАН, Москва.
Введение Попутные
газы (ПГ) на нефтяных месторождениях являются ценным углеводородным сырьём, для
любой отросли промышленной инфраструктуры.
ПГ эффективно используются, если месторождение находится относительно
близко к тепловой электростанции или химическому перерабатывающему предприятию
[1]. Однако в России на удалённых месторождениях ПГ никак не используются, а
сжигаются. Причем экологический вред от такой практики заметен на больших площадях. На
удаленных от промышленных структур нефтяных месторождениях для переработки ПГ
требуется, чтобы конечный продукт переработки ПГ имел реальную коммерческую
ценность и мог быть использован в инфраструктуре месторождения. Необходимо
также, чтобы оборудование, используемое для утилизации ПГ, было мобильным (для
перевода на другое месторождение) и органично связано с основными задачами
месторождения [2]. По оценкам,
наибольшей и реальной коммерческой ценностью будет производство из ПГ
экологически чистого бензина и дизельного топлива (ЭБДТ) [3].
Самой сложной и ответственной частью реальной
технологической схемы переработки ПГ
является получение из ПГ чистого синтез газа (смесь Н2 и СО)[4]. Эта смесь должна использоваться в процессе
Фишера-Тропша для синтеза ЭБДТ. Однако, если синтез газ (СГ), полученный из ПГ, из которого по методу Фишера-Тропша
получают ЭБДТ, содержит более 15%
массовых газовых примесей кроме СО и Н2, то скорость реакции на
катализаторе будет очень малой и процесс синтеза углеводородов заданного
состава будет медленной и соответственно нерентабельной [5]. Решение задачи
получения СГ для синтеза ЭБДТ в рамках инфраструктуры удаленных месторождений
нефти можно использованием специального метода прецизионной каталитической
конверсии углеводородов (ПКК) [6]. Под ПКК понимается проведение каталитической
конверсии в обогреваемой трубе с использованием перегрева реагирующего
углеводорода на ингибиторе и индивидуально регламентированным обогревом трубы
заполненной ингибитором и катализатором электротоком пропускаемом через трубу и
осуществление каталитической конверсии при стехиометрическом отношении
углеводород/окислитель. Обогрев должен осуществляется
прямым пропусканием электрического тока через трубу, на разных участках с
заданной интенсивностью. Каталитическая конверсия углеводородов в обогреваемых
трубах является базовым процессом в химических производствах и стоит в ряду
самых энергоёмких процессов. На обогрев труб заполненных катализатором, где
происходит образование СГ, затрачивается много природного газа. Для
энергосбережения отдельные трубы собираются в агрегаты, содержащие 500 и более
труб конверсии. На этих устройствах невозможно обеспечить, использованием
газовых горелок, равномерный и строго заданный обогрев трубы по длине и по
окружности [10, 11]. Обеспечение необходимого заданного и регулируемого
теплового потока на отдельной трубе с помощью горелок, крайне затруднено
[12,13], поэтому конверсию природного газа осуществить при отношении близким к
стехиометрии
(эквивалентный метан)/(окислитель) < 1,5 теоретически не возможно[7]. Как показано в [7] осуществление
стехиометрической конверсии углеводородов без избытка окислителей (Н2О
и СО2), т.е. в стехиометрии,
не возможно без обеспечения подачи тепла в катализатор в зонах наиболее
активной реакции. Необходимый прецизионный подвод тепла можно обеспечить только
с помощью трубы, через стенку которой пропускается электрический ток.
Экспериментальное
исследование передачи тепла от стенки трубы к слою катализатора при прямом
электрическом обогреве.
Эксперименты по нагреву трубы заполненной никелевым
катализатором, прямым пропусканием электрического тока представлены в работах [7], [8], [9]. На рис.1 показана труба реактора для
исследования стехиометрической конверсии метана с использованием прямого
электрического обогрева. Труба имела
длину 1,5 м, внутренний диаметр был
54мм, толщина стенки 3мм, сталь
45Х25Н20С. На входе в трубу подавалась смесь СН4 и Н2О
(СМВ). Со стороны входа размещался слой ингибитора, где смесь СМВ нагревалась
без реакции до температуры стенки.
Далее труба заполнялась катализатором, где происходило превращение СМВ
в водород и окись углерода, т.е. в СГ. На трубе испытывалась эффективность передачи тепла от стенки к слою катализатора изменением теплового потока
посредством электрического тока. Ток подавался трансформаторами ОСУ и
регулировался РНО. Труба имела теплоизоляцию из асбовермикулита и каолиновую вату диаметром 0,4м. Тепловой поток
в окружающую среду не превышал 5 Вт/м2.
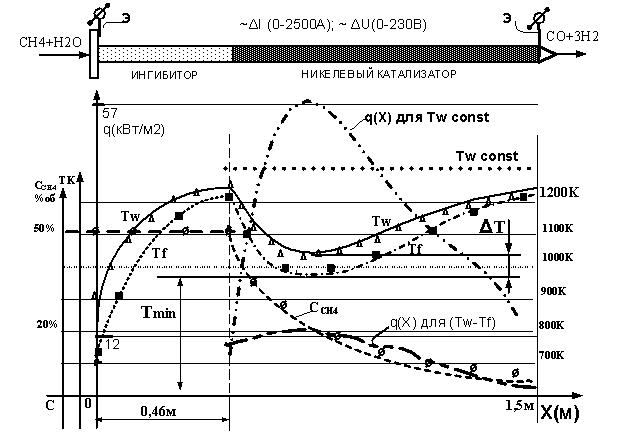
Рис.1 Труба реактора для исследования эффективности переноса
тепла от стенки, обогреваемой прямым электрическим обогревом. Э – электроды. Tw , Tf – температуры стенки и газа. q(X) –
тепловой поток от стенки к реагирующему газу для равномерного обогрева и для
гипотетического случая, когда Tw – const.
На рис 1 видно характерное развитие температур реагирующего газа и
стенки трубы по длине слоя катализатора. Этот эффект описан в [7] и [8]. Эффект
падения температуры после границы ингибитор-катализатор (ГИК) наблюдается во
всех режимах протекания через обогреваемую трубу исходной смеси СН4(метановый
эквивалент углеводорода) с Н2О и СО2 . При падении
температуры после ГИК температура падения
реагирующей смеси достигает некоторого минимума Tmin =
(1000±40)K (МТПРС).
Величина МТПРС зависит: 1) От максимальной температуры стенки на границе
ингибитор-катализатор, 2) От формы гранул катализатора, 3) Массового расхода
исходного газа и 4) отношения (Н2О
и, или СО2) ⁄ СН4.
Это основные параметры, влияющие на функцию падения температуры после
ГИК. Согласно физическому смыслу
исследуемого процесса МТПРС зависит от ряда параметров (например, активности
катализатора), но интенсивность их воздействия на МТПРС не велика в сравнении выше
перечисленными формами воздействия и соответственно теряются при специальных
измерениях и расчетах.
На рис.1 видно, из характерной формы кривой реагирующего
газа, что кривая падения концентрации метана на участке 6-8 калибров после ГИК
поглощается более 50% всего тепла идущего на конверсию [7-9]. Во всех
исследованных режимах кривые изменения температуры стенки и газа после ГИК
имеют характерную параболическую форму и могут быть описаны полиномом 4-й
степени, как функция Т = f (X), где Т – температура, Х – координата
определяющая длину слоя катализатора в интервале 0,46 – 1,5 м на
экспериментальной трубе. Функция для температуры газа и стенки:
Т(Х) = a + b x + c x2 + dx3 + ex4 ,
где a, b, c, d, е –
зависят от параметров проведения эксперимента, которые определяются отдельно
для Tw(Х) и Tf(Х). По формуле определения теплового потока:
q(X) = α ∆T(X),
где α –
коэффициент теплоотдачи от внутренней стенки к газу и ∆Т(Х) = Tw (Х) – Tf (Х) в пределах интегрирования Х1=0,46м и Х2
= 1,5м. Получим функцию q(X).
Для Tw : a=4209.9875, b=-–12655.055, c=18056.138,
d=-–10930.554, e=2427.6151, для Tf
: a = 3874.7824, b = –
11258.153, c = 15605.529, d= – 9122.4311, e=1960.9168 функция q(X) будет следующей: q(X)=q(x)=67040-2.793804e5*x+4.901218e5*x2-3.6162458e5*x3+93339.66*x4
. На рис.1 видно, что максимум
мгновенного значения теплового потока (12,4кВт/м2) кривой q(Х) для (Tw-Tf)
соответствует наибольшему ∆Т. Интегрирование полученной функции в пределах 0,46 – 1,5м дает
мощность 8,2 кВт снимаемую реагирующим газом со стенки трубы, что соответствует
массовому расходу иллюстрируемого эксперимента и мощности подводимой к трубе
(расход метана = 9×10-4моль/с или объёмная скорость = 1350ч-1, 1200А и 6,9В). Очевидно, что если увеличить средне интегральный
∆Т, то тепловой поток возрастет. На рис.1 точечной пунктирной прямой
линией q(X) для Tw const обозначена гипотетическая постоянная температура стенки
равная максимальной рабочей температуре металла обогреваемой трубы 1300К. В
этом гипотетическом случае средне интегральная ∆Т будет наибольшей. Также
как и для первого экспериментального случая получена функция распределения
теплового потока q(X) для Tw. Максимальное мгновенное
значение q(X) для Tw равно 57кВт/м2, полная снимаемая мощность 36,2кВт. В этом случае процесс
должен проводился при расходе метана 48×10-4моль/с или объёмной скорости 5900ч-1. (В промышленности объёмные скорости более
2000 ч-1 не возможны, т.к. внешний обогрев сжиганием газа не может
обеспечить необходимого коэффициента теплопередачи с наружи трубы, а внутренний
коэффициент теплопередачи значительно превышает α от продуктов сгорания к внешней
поверхности трубы [10],[11],[12].)
Согласно полученным результатам проведены
эксперименты, результаты которых представлены на рис.2. Труба
разделена на 3 отдельно нагреваемых током участка, которые индивидуально
обогреваются через 4 электрода через
трансформаторы типа ОСУ и РНО.
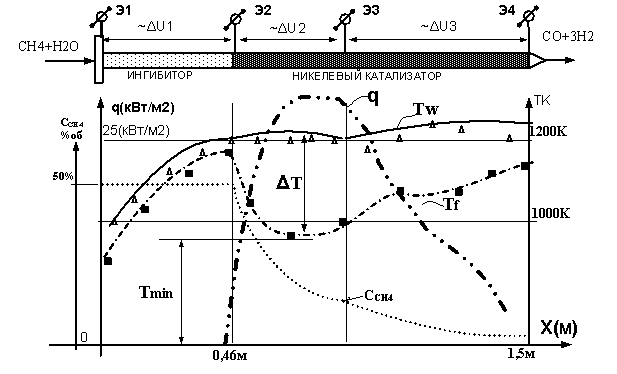
Рис.2 Обогрев трубы 3 отдельными обогреваемыми участками прямым
электрообогревом. Э – электроды, Тw – температура стенки эксперимент
обозначен - ∆, расчет сплошной линией; Тf – температура газа эксперимент обозначен - ■, расчет
линией точка-тире. Расчетное распределение теплового потока q обозначено линией точки-тире.
На рис.2 представлен эксперимент, где расход метана был 41×10-4 моль/с или объёмной скорости 5040 ч-1 при отношении Н2О
⁄ СН4 = 1. Общая
электрическая мощность, подводимая к трубе, была 31кВт. Для расчета
распределения температуры в слое катализатора и распределения определения
функции q(X) на протяжении всей трубы использована квазигомогенная модель [7].
Расчет для участков Э2 – Э3 и Э3 – Э4
распределения температуры проведен отдельно. Функция q(X) рассчитана для участка Э2 – Э4.
Таким образом, экспериментально показано, что обогрев трубы
прямым пропусканием электротока обеспечивает высокую эффективность снятие тепла
от стенки в слой катализатора и как следствие возможность осуществления
каталитической конверсии газообразных углеводородов в стехиометрическом отношении
без разрушения катализатора углеродом разлагающихся углеводородов и с большой
производительностью получения чистого СГ. Использование в реальной
технологической схеме утилизации ПГ на удалённых нефтяных месторождениях ПКК
позволит производить ценные экологически чистые бензин и дизельное топливо.
Технологическая схема утилизации ПГ в ЭБДТ на основе ПКК.
Ясно, что наиболее ценным продуктом переработки ПГ будут
экологические чистые бензин и топливо на основе ПКК. Покажем это на основе уже
имеющихся в нефтеперерабатывающей и нефтедобывающей инфраструктуре способах и
устройствах. Проблема заключается в реальном осуществлении получения СГ для
получения ЭБДТ. В ПГ содержится от 20 до 60%
газообразных углеводородов (С6H12 , iС6H12 , …. С2H6 )
более высокого порядка, чем СН4.
Поэтому получение СГ нужно проводить в два этапа [14]. Каталитическую конверсию
углеводородов с водяным паром можно
описать следующей химической формулой:
СnHm + nH2O = n CO + (2n+m)/2 H2 (1)
Для расчетов пользуются формулой, где СnHm заменяется метановым эквивалентом [7], [9], [10]:
ε СН4 + β
Н2О + 204 кДж/моль = γ
СО +
3δ Н2 (2)
Где ε, δ, γ, β - коэффициенты перевода в метановый
эквивалент:
СnHm → …… → С2H6
→ С2H4
→ С2H2
→ СH4 (3)
Для расчетов уравнение (1) приводится по метановому
эквиваленту к формуле (2) согласно цепи превращений (3) по методикам [9] и [10].
Далее расчет по заданным начальным и граничным условиям первого рода ведётся
согласно квазигомогенной модели [7] .
Основная
задача первого этапа осуществить
превращение углеводородов высокого порядка в метан по схеме (3).
Происходит также частичная конверсия углеводородов (до 40%) в СГ [13,14,15] . Это
устройство загрузки инертной и каталитической насадок было испытано на трубе с промежуточным
перегревом для паровой конверсии углеводородов фракции С1÷С5
в ПГ установленной в трубчатой печи Коксогазового завода ПО
«Ангарскнефтеоргсинтез» [8,14]. Такая труба в формате ПКК имеет длину 7 м
показана на рис.3.
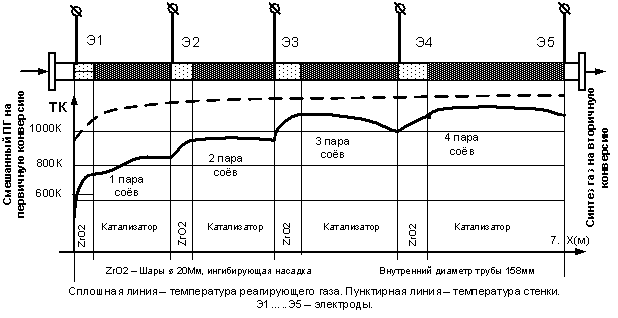
Рис.3 Труба для паровой конверсии в трубчатой печи Коксогазового завода ПО
«Ангарскнефтеоргсинтез» с прямым подводом электротока.
Состав смеси газов на вход в трубу первичной
конверсии: ПГ после очистки, водяной пар, остаточная смесь газов с аппаратов Фишера-Тропша
после синтеза бензина и дизельного топлива. Нагрев трубы ведётся 4 парами
электродов – Э1-Э2, Э2-Э3, Э3-Э4 и
Э4-Э5. Регулировка электротока осуществляется согласно заданным расходным
параметрам. Температура стенки должна быть не более 1100К. На выходе из трубы
смесь газов уже не содержит углеводородов фракций С2 – С5, а содержит водород, окись углерода, метан и
не прореагировавший водяной пар. Эта газовая смесь поступает на вторичную
конверсию.
Труба
вторичной конверсии изображена на рис.4.
Особенность второй трубы проведение конверсии, это прецизионное
осуществление стехиометрической конверсии. Показанная на рис.4 труба выполнена
аналогично экспериментальной трубе показанной на рис.2, но с большим
количеством электродов. В процессе эксплуатации трубы работают следующие пары
электродов: I-VI, I-III, II-III, III-IV, IV-V. Электроды
могут перемещаться и выдерживать максимальную технологическую температуру
стенки трубы. На выходе из трубы образуется синтез газ состоящем практически
только из СО и Н2. Согласно термодинамическим параметрам процесса
содержание других газов не превысит 3%.

Как указывалось выше из независимых
источников [1,2,3,4,21] известно, что
для реального получения ЭБДТ из ПГ
необходимо решить проблему стехиометрического превращения углеводородов в
синтез газ. Выше экспериментально показано, что технически эта проблема решена.
Поэтому опять же согласно независимым
источникам [11,12,17,18,19,21,22,] предлагается полная технологическая схема
получения ЭБДТ из ПГ на удаленных нефтяных месторождениях. В схеме, все аппараты и технологии
переработки ПГ отделенных процессов,
кроме двух труб конверсии углеводородов, используются в настоящее время в
промышленности [18],[19], [20]. На рис.5 показана схема получения ЭБДТ для
случаев, когда массовый расход добываемой нефти составляет 80 – 350 т/сутки.
Такой интервал связан с габаритными и весовыми параметрами используемых
аппаратов и машин, т.е. эксплуатируемые устройства могут быть перемещены на
автомобильных платформах или на воздушном транспорте. Если расход менее 80
т/сутки меняются размеры аппаратов, если добыча нефти превышает
350т/сутки, устанавливается двойная
параллельная система.
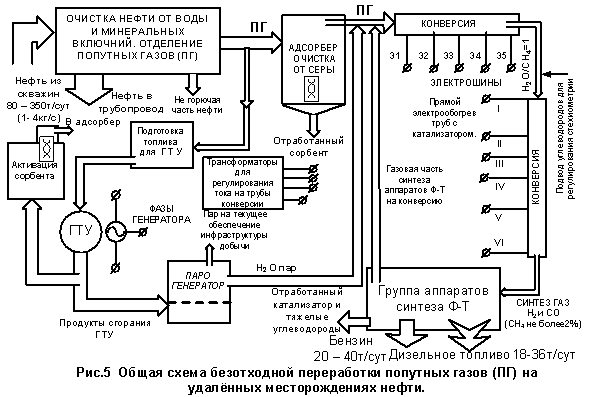
На схеме нефть из скважины поступает в
технологическую систему, где происходит первичная очистка нефти. На рис. 5 эта система аппаратов обозначена
прямоугольником – «Очистка нефти от воды, минеральных включений и отделение
попутных газов». Оборудование используется по рекомендациям [19, 20, 21] апробированными
аппаратами на действующих скважинах. ПГ разделяется на два потока. Малый поток
(~30% от всего потока ПГ) идет на получение электроэнергии для обеспечения
подачи тепла на ПКК и обеспечения основных нужд месторождения. Для этого нужно
использовать газотурбинные электростанции (ГТУ) [22]. Отходящие газы ГТУ
используются для получения водяного пара в парогенераторе для ПКК и для
активизации сорбента очищающем ПГ от соединений серы. В качестве сорбента
используется дроблёный известняк [16]. Известняк обрабатывается в аппарате-активизаторе
сорбента горячими продуктами сгорания ГТУ. Сорбент переводится в адсорбер. Из
адсорбера чистые ПГ смешиваются с водяным паром и газовыми остатками синтеза в
группе аппаратов Фишера-Тропша (Ф-Т). Полученная газовая смесь поступает на
первичную конверсию ПГ, где труба обогревается электротоком, получаемым с
генератора ГТУ через трансформаторный стационар. В первой трубе конвертируются
углеводороды более высокого порядка, чем метан. Далее газы поступают в трубу
вторичной конверсии, где происходит образование синтез газа (СГ) состоящем из
СО и Н2 , поступающих в группу аппаратов синтеза Ф-Т. При содержании
в СГ до 98% СО и Н2 синтез Ф-Т углеводородов заданного состава можно
вести на дешевых окисно-железных катализаторах[17,18]. Отработанный катализатор
из аппаратов Ф-Т и отработанный сорбент используется в дорожной логистике
инфраструктуры месторождения. Полученные бензин (20 – 40 т/сут) и дизельное
топливо (18 – 36 т/сут) в направлении применения проблем не имеет. Данные интервалы
производства бензина и дизельного топлива зависят от количества нефти и
содержания в ней ПГ.
Масса единицы оборудования ПКК (2 трубы)
не превысит 4т. Другие объекты технологической схемы имеют массу не более 10т.
Все объекты технологической схемы в случае необходимости перемещения могут быть
разобраны и перемещены на автоплатформах или авиационной технике.
Заключение.
1.
На основании
представленных экспериментов можно утверждать, что производительность
каталитической конверсии углеводородов в обогреваемых трубах с нагревом прямым
пропусканием электротока значительно выше, чем труб обогреваемых сжиганием
природного газа. Так в экспериментах при прямом электрообогреве, объёмная
скорость по конвертированному метану превышает 5000 ч-1, а в трубах
обогреваемых продуктами сгорания, такая же объёмная скорость теоретически не
может превышать 2500 ч-1.
2.
Прямой электрообогрев
труб позволяет обеспечить подачу необходимого тепла на сильно эндотермическую
реакцию конверсии за счет постоянной температуры по длине и окружности трубы.
Такая технология позволяет провести стехиометрическую конверсию углеводородов
на трубах с промежуточным перегревом, без аварийного выделения углерода.
3.
Исходя из оценки затрат
на производство из ПГ наиболее рентабельного продукта разработана реальная
технологическая схема утилизации, которая может успешно работать на удаленных
нефтяных месторождениях.
4.
Устройство электрического
обогрева труб каталитической конверсии может быть использовано во всех технологиях,
где необходимо получать СГ из углеводородов.
Литература:
1.
Андрейкина Л.В. «Состав,
свойства и переработка попутных газов нефтяных месторождений западной Сибири»,
Автореф. на соиск. к.т.н. , НИИРеактив, Уфа, 2005.
2.
Юлмухаметов Д.Р.,
Афанасьев И.С., Мухамедшин Р.К., Вавилов Н.В., «Интегрированная методика
расчета показателей разработки нефтяных месторождений для формирования
бизнес-плана», «Научно-технический вестник ОАО «Роснефть»» июнь 2010
3.
Гулейкова Н.Г. «Будем
топить по белому», ГАЗПРОМ, №11, 2004.
4.
Курбатов Н.И., Зайцев
А.К. «Конверсия природного газа в жидкое топливо», Потенциал, №3, 2002.
5.
Калечиц И.В.
«Моделирование ожижения угля», - М. ИВТАН, 1999.
6.
Игумнов В.С., Визель
Я.М. Прецизионная каталитическая
конверсия углеводородов для питания твёрдо-оксидных топливных элементов// VII
Международный форум «Высокие технологии XXI века», Москва, 23-26 апрель 2007.
7.
Igumnov V.S. “Technical and technological methods of realization of
steam catalytic conversion of natural gas with a methane-water proportion close
to stoichiomythic ratio” , Hydrogen materials science and chemistry of carbon
nanomaterial, NATO security science setias – A: Chemistry and Biology, The NATO Programmer for Security through
science. Page 555-561. 2007.
8.
Игумнов В.С., Визель
Я.М. «Каталитическая конверсия углеводородов в обогреваемой трубе при отношении
пар/газ близком к стехиометрическому»; Катлиз
в промышленности, №6, 2010, с34-40.
9. Igumnov V. S. ,
Vizel Ya. M. «Catalytic Conversion of Hydrocarbons in a Heated Tube at a Nearly
Stoichiometric Vapor to Gas Ratio» CATALYSIS IN INDUSTRY ,Vol. 3, No.1, 2011
10. Справочник азотчика: Физико-химические свойства газов
и жидкостей. Производство технологических газов. Синтез аммиака. – 2-е изд.,
Т.1, М.: Химия, 1986.
11. Справочник по теплообменникам, Т1 и Т2, пер. с англ.
Под ред. Б.С. Петухова, В.К.Шикова – М., Энергоатомиздат. 1987.
12. Тепловой расчет котельных агрегатов (нормативный
метод), под ред. И.К. Кузнецова, В.В. Митора, И.Е. Дубовского, Э.С. Красиной –
М., Металлургия, 1983.
13. Распутько В.М., Челюк Г.И., Нестёркин В.Н., Селицкий А.П.,
Веселов В.В. «Испытание катализаторов паро-углекислотной конверсии природного
газа», Химическая технология (Украинский журнал), № 4, 1985, с16-29.
14. Vizel Ya. M. “The
catalytic conversion of the oil processing gas with intermediate heating “. (1550) 10-th International Congress CHISA-90. Praha,
Czechoslovakia, August 26-31, 1990.
15. А.с. 18299181 СССР, МКИ 4В 01D 53/54, Устройство для
паровой каталитической конверсии нефтезаводских газов/ Я.М. Визель, В.Е. Ванин,
В.Г. Липович, С.В. Гусаров, Г.И. Дружинин, В.И. Кириллов, приоритет 23.06.89.
Опубл. Бюл. №28, 16.05.90.
16. Альтшулер В.С. «Газовые процессы», - М. , Наука, 1987
17. Дигуров Н.Г., Каган Д.Н., Королёва Н.В., Кречетова
Г.А., Михайлова О.А. «Трехфазный синтез Фишера-Тропша», Препринт ОИВТ РАН №
8-498. – М. 2009.
18. Печуро Н.С., Капкин В.Д., Песин О.Ю. «Химия и технология синтетического жидкого топлива и газа». – М.
: Химия, 1996.
19. 13-я Международная выставка «Оборудование и технологии
для нефтегазового комплекса», М., Экспоцентр – выставочный комплекс на Красной
Пресне, 21-25 июня 2010, Каталог.
20. «Промышленная продукция для нефтегазового комплекса»,
Технический каталог нефтегазового оборудования с информацией о поставщиках,
Фирма OIL-GAS, М., 2009.
21. Маргулов Р.Д., Хачауров В.Р., Федосеев А.В. Системный анализ в перспективном
планировании добычи газа. – М.: Недра, 1992
22. Цанев С.В., Буров В.Д., Ремезов А.Н. Газотурбинные и парогазовые установки
тепловых электростанций. – М., изд. МЭИ. 2009.